
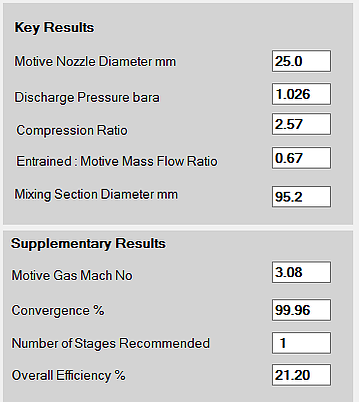
Refinery vacuum distillation towers use ejector systems to maintain tower top pressure and remove overhead gases. However, process conditions, supplied utilities, corrosion, erosion and fouling all have an impact on ejector system performance. These vacuum systems normally provide reliable and consistent operation. Routinely surveying tower overhead vacuum systems can improve performance and product quality. The hybrid vacuum source is reliable, requires only routine maintenance, and will contiue to save substantial amounts of steam each year compared to the five-stage steam jet ejector. The jet ejector/liquid ring vacuum pump system has provided both the capacity and the extremely low vacuum needed for the polyester polymerization vessel, after making a small modification. The liquid ring vacuum pump would increase the material and installation cost of the system by about $4000, but the savings in steam consumption would pay back the added cost in less than two years. The hybrid system was selected because the three-stage jet ejector would use only 1240 lb/hr of 100 psig steam. The other option was a hybrid vacuum source composed of a three-stage steam ejector system and a liquid ring vacuum pump that is more energy efficient than ejectors for low vacuum applications. A new five-stage jet ejector system to meet these requirements would use 1395 lb/hr of 100 psig steam.

Two options were considered when the company decided to replace the original system with a system designed for 0.15 mm Hg more » with a non-condensible gas load of 10.8 lb/hr. A consistent polymerization vessel vacuum of 0.3 mm Hg is needed, but the existing vacuum source, a five-stage steam jet ejector, could only provide a 0.5 mm Hg level. The process for making polyester requires an extremely low vacuum on the polymerization reactor. Nylon-6 molding and extrusion resins are also produced at the plant in Hopewell, Virginia. = ,įirestone Fibers and Textiles Company, a division of Firestone Tire and Rubber Company, manufactures tire and industrial yarns of polyester and nylon-6. The 12 appendixes cover: physical properties of common fluids handy vacuum engineering data and rules of thumb SI unit conversions sizing air and steam metering orifices for testing drill sizes ejector operating costs and design optimization forms for ejector calculations, tests, and inspections instructions for preparing ejector specifications test kit contents list ejector manufacturers and suppliers of referenced hardware and information and failure modes and symptoms. Upgrading of existing ejector procedures and hardware is reviewed in Chapter 12. Chapter 11 reviews steam-jet refrigeration, steam-jet and gas-jet compressors, liquid jet eductors, desuperheaters, special design situations, and designing one's own more » systems. Part 4 on other ejector applications and upgrading ejector usage also consists of two chapters. Part 3, consisting of two chapters, is devoted to specifying and purchasing steam jet ejectors. The final chapter of Part 2 (Chapters 3-8) thoroughly covers all aspects of operation, testing, troubleshooting and maintenance. Chapter 7 is an excellent review of installation of ejector vacuum systems. The various types of pressure control are discussed in Chapter 6. In Chapter 5, contact and surface condensers are reviewed, and calculation procedures are presented.


Engineering calculations for ejector stages is thoroughly discussed in Chapter 4. How ejector stages work is reviewed in Chapter 3. Chapter 2 discusses what an ejector is and how it works.
#Ejector design calculation software how to
Chapter 1 is a short overview on how to use the text. There are still many applications, however, such as those with large capacity requirements, where ejectors are the only equipment that can produce sufficient vacuum. With increasing emphasis on stricter pollution control, their use was curtailed. Steam jet ejectors were for many years the workhorse of the chemical process industries for producing vacuum.
